The blowing film extrusion system is one of the most complex and sensitive of all plastics processing technologies. Good film appearance is the result of the right combination of raw materials, equipment, and process.
When you see the dot or unexpected things in the blowing film, it may be caused by the contamination. The contamination can come from raw materials or during the processing.
1) Raw material – the first factor in blowing film
Raw materials quality is initially controlled by the suppliers. The raw materials must meet the customer’s requirements for physical properties, additive levels, etc. However, even though the raw materials are good, there are additional opportunities for it to be contaminated. First by residual material in the transfer system, and second, by residual material in the container itself. Stones and dirt from outside are often removed from the screen packs of many extruders. Raw materials stored in fiber drums or boxes without lines can pick up cellulose fibers that can result in gels.
If colorants or filler masterbatch are used, the appearance of the film is dependent on a thorough dispersion. That dispersion can get via a good mixing screw, assuming there is good master-batch mixed with the resin prior to extrusion. Poor dispersion shows clouds of color or dots in the film. Which can result in heat seals with variable strength as the amount of color or filler and film density varies in the seal area.
Good suppliers can help in this chapter. Fillplas is supplying good qualities filler masterbatch for blowing film with standard packing with liner. It ensures quality and avoids contamination.
2) The processing of blowing film – the main factor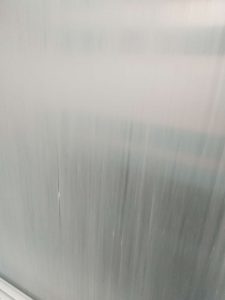
Even though the raw materials are good and clean, it still can be contaminated in processing. The source of contamination is dirty, unchanged filters in raw materials transport systems and the upper inner surfaces of extruder hoppers coated with layers of dust from many different materials previously used. These materials can intermittently fall into the extruder and contaminate materials in the system.
Contamination also can come from inside the extruder by a new material gradually purging an old, degraded material from stagnant areas in the system. A die which has been overheated or that has not been cleaned often can cause gels in the film, particularly when new material is introduced to the system. In both cases, the gels are usually random throughout the film and can be clear to amber to black in color and look like tapioca and/or arrowheads. Gels from a burn in the die web, equipment, process or from a point inside a side fed die where two melt flows join, appear only in one area of the film. Again, one or more floodlights mounted to illuminate the frost line and the melt below it can also help operators identify and determine the type or origin of the gels.