In nearly all applications of plastics in packaging, the first step is to convert the solid plastic, usually in pellet form, into a melt. This melt can then be shaped using heat and pressure into a useful form. The equipment used to do this is an extruder.
What is the extruder?
An extruder is used for film and sheet, and is part of a blow molder for bottles. An extruder is also part of an injection molding machine for injection molded or injection blow molded packaging. The extruder used in all of these applications work in a similar manner. But they deliver the melt to the shaping operation differently. We will explore these differences as we proceed.
How it works?
The purpose of an extruder is to use heat, pressure, and shear to transform the solid plastic into a uniform melt, for delivery to the next stage of processing. This frequently involves mixing in additives such as color concentrates, blending resins together, and incorporating regrind. Regrind is the granulated scrap from the conversion process. The final melt must uniform in temperature and in composition. Because single screw extruder are often not very good mixers, an additional mixing device may be needed. The pressure of the melted viscous polymer as it exits the extruder must be high enough. Which force it through a die to produce a desired shape, or to force it into a mold chamber.
The extruder accomplishes all this by using a barrel, a hollow tube, containing a screw with helical channels.
A simplified extruder diagram is shown in Figure 1, and details of a screw are shown in Figure 2.
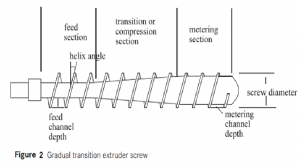
The screw generally divided into three sections: (1) the solids conveying section, (2) the compression or melting section, and (3) the metering or pumping section. The standard single screw extruder has a right-hand helix on the screw. The screw rotates in the counterclockwise direction. If one thinks of a standard wood screw, which also right hands, turning counterclockwise. While it holds stationary in space, the wood moves toward the screw tip.
Others
The same action occurs in the extruder. The basic screw design has only a single flight, but other designs have double flights along part or all of the screw length. Other important components are the hopper, which feeds the plastic or other components into the extruder through the feed port, and the die or nozzle, through which the melted plastic exits the extruder.
FILLPLAS developed many Grade with PP resin for extrusion and injection.
For further information, please send offer through info@fillplas.com.