General
In the 1800s, the advent of plastics and polymers spawned the concept of injection molding. The basic definition of injection molding is easy to understand. In the case of plastic injection molding, plastic resins, sometimes referred to as “plasticizers,” are passed through a heated plastic injection mold to create specific product forms. Under heated temperatures, these resins become pliable and elastic enough to transfer to molds. One example of injection molding is the method by which window lineals are producing. In this example, polymerized plasticizer resins are entering into a heated industrial hopper and transfering through a screw or clamp type output to a plastic injection molding machine with sprue and ejector controls.
The heated elasticized material is shaping into long rods by the injection mold process. The injection mold may design with decorative curves and angles, or the injection mold may include small markings. Therefore, these markings indicate where the rods will join so fabricators can attach these to window glass to create window frames. Moreover, some injection molding machines also have cooling chambers where high heat temperatures are requiring to create the final product.
A Plastic Injection Process With Many Uses
Today, a plastic injection mold is using to create rubber, metal and plastic products. These products include: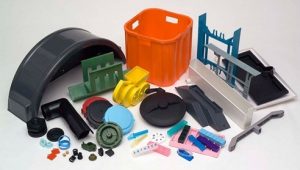
- Toys
- Computer hardware
- Housing for small household appliances
- Bottles
- Vinyl home siding and windows
- Automotive parts like ball bearings, dashboard panels and sparkplugs
A Plastic Injection Mold for All Your Needs
It’s possible to
find a product in every home, business, office or manufacturing plant that has a number of injection molded products. Beauty accessories like combs, hair brushes and the housings for blow dryers are examples of these products. For instance, outdoor picnic tables, chairs and chaise lounges and implements like garden rakes are also producing through the molding process. Otherwise, milk, soda pop and laundry detergent bottles are another group of products. This particular group of products requires food grade quality plastic resins that are safe for human use. Fillplas uses the resins for food grade quality items are blended with biocides to protect humans from exposure to bacteria when these bottles are filled with various organic liquids