GENERAL
Woven polypropylene bags (PP woven bags) are the alternative to disposable plastic bags mainly used by retailers. They are well known for their strength ensured by a specific mesh covered by a plastic layer. By this way, these bags are solid, waterproof and washable and they have convinced a large majority. In fact, the polypropylene bag has become more and more famous since the last decades especially thanks to its durable and sustainable features for the environment.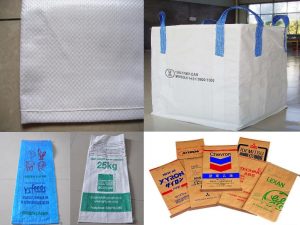
These bags are more eco friendly than typical plastic bags and they are more convenient and more resistant. Generally, these woven polypropylene bags use in order to pack different kind of items as foods, cement or chemical products for example. This range of bags can indefinitely decline according to dimensions, thickness, strips, closures, choice of printing or lamination. However, these woven polypropylene bags has to keep away from the sun because this material can be deteriorated under the sun light. In addition, these bags define according to their color, the non-slip treatment and the UV protection. Then, the purpose categorize the load in kg, the volume in litre, the density of the content and the grain size of the content.
PRODUCTION PROCESS
To manufacture these bags, several steps and several machines are necessary.
The process is as simple as rigorous and requires frequent quality controls. Extrusion is the first step needing to make these bags. It consists in transforming a polymer (in the form of granulate or thermoplastic powder) into a long thread of variable thickness depending on the final product (cables, tubes, sheets, films, textile fibers, plates, bags, etc.).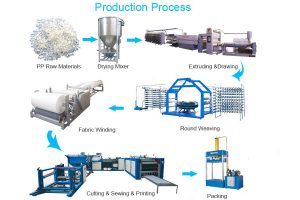
For the manufacture of plastic bags and films, blow film extrusion is used. The raw material then melt and stretch in order to form a film of a defined thickness. This will then be cooled by a thermostatically controlled roller. Once completed extrusion, the next step is to wrap smoothly and steadily over the plastic strips in order to form rolls. These roller used for the next stage, the weaving of polypropylene thanks to the circular looms. It is a specific equipment that produces woven fabrics based on flat tube-shaped polypropylene threads. Once these tubes have obtained, the next step is to print the colors, inscriptions and images ordered by the customer. This step gives the bag a personalized design according to the defined instructions. To do this, the patterns printed on the bags with an ink pad. Then, cutting and sewing remains. To cut the bags according to the specific dimensions, the equipment program. However, for the sewing the human know-how need.
More useful, more convenient, more eco-friendly and stronger, these bags are a good deal for the daily life.
FILLPLAS has many grade of filler masterbatch for PP woven bags, we have also developed for PE woven bags.
For more information, please contact us at info@fillplas.com